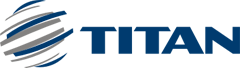
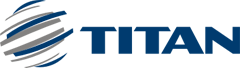
Managing risks is a way of being more proactive and increasing our competency and capacity to adapt effectively to a changing business environment. TITAN Group therefore continuously expands the scope of risk assessment processes to achieve greater understanding both of our opportunities and the changing concerns and expectations of key stakeholders.
Managing risks and associated opportunities is a fundamentally important part of TITAN Group’s long-term sustainability. Accordingly, the financial and non-financial material risks that the Group is exposed to are addressed at the highest level, during an annual presentation by the CFO to the Board of Directors. Risk management can be broadly defined in several major categories: material risks that the Group can have some control over (such as biodiversity), material risks that are beyond the Group’s control (such as the political risk in Egypt) and medium-level potential risks that are not currently material to our business but could become so, such as human rights abuses.
The Group has systems in place to monitor and anticipate potential material, social and environmental risks that are similar to those used to mitigate financial risks. We work continuously to ensure that our risk monitoring systems are refined, as outlying issues become potential threats to our operations, such as water shortages in certain areas of our operations.
Acknowledging social and environmental risks among the most material for TITAN’s business, relevant audits and management reviews are conducted every year in all production plants following ISO requirements. Moreover, in 2011, a new process was launched at Group level to provide an overall assessment and benchmark of potential health and safety risks (while the existing tool for the assessment and analysis of environmental risks was further enhanced). The only exception was SharrCem, which was scheduled to be included in the Group-wide risk assessment process in 2012, but which had to be cancelled due to necessary stoppages in the operation of the plant after the middle of the year. In all other plants, the risk assessment was conducted as planned.
In 2012, a step further was taken with respect to human rights risks, as a commitment undertaken by TITAN, in its capacity as a core member of the U.N. Global Compact Initiative. Although for TITAN operations, the risk of human rights abuses is estimated to be a moderate risk, to assess TITAN’s readiness and maturity in addressing these risks, an evaluation of relevant policies and grievance mechanisms employed by the company was completed in co-operation with CSR Europe. This evaluation was made using the recently adopted U.N. Human Rights Guiding Principles on Business and Human Rights (Ruggie Framework).
Along with our partners in the cement industry, we recognize that social and environmental risks to and from our operations are plentiful, multifaceted, and complex and require a coordinated approach. This was a key driver for the foundation of new Working Team in 2012 that is focused on sustainability in the supply chain. (see relevant case study here). TITAN acknowledged this need as early as 2006, when it was engaged as a co-leader in the thematic workshop for CSR in the supply chain together with three other European enterprises jointly representing four sectors: cement and construction materials, automotive, IT and cosmetics. It was this joint effort that resulted in the development of the first ever online portal for information and guidelines supporting the commitment to corporate social responsibility throughout the value chain (See Supply Chain Laboratories in 2007’s report, page 53)