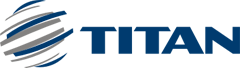
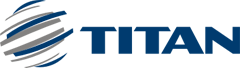
Climate Change, Energy and Resources - an Every Day Challenge
- TITAN Group Climate Mitigation Strategy
- GAEA case
- Environment and alternative fuels
- Raising environmental awareness to improve performance
- Launching collaborative action for environmental education
- Stakeholder engagement and public consultation
- Meeting high environmental standards
- Environment: Green Belt Near Kosjeric
- WBCSD/CEMENT SUSTAINABILITY INITIATIVE: 10 years of progress - moving on to the next decade
- Voluntary Sectoral Agreement: Public-Private Partnership in the Cement Industry in Greece
Climate change is strongly affected by the way we use our resources and the environment as a whole. For the energy-intensive cement and construction industries, energy and raw materials are fundamental. For many years, these industries have invested in Research and Development, creating new methods and practices to offer reliable solutions for society and the environment.
Energy efficiency and the conscious use of raw materials that is aligned with a waste management system, as described by the Reduce, Reuse and Recycle schema, is a proven opportunity to add value throughout the value chain, particularly at the local level. Relevant examples of such practices are given through all the areas we currently operate.
Reducing our environmental footprint was, and still is, one of our main concerns and the focus of our determined efforts. In a changing world, keeping on track with our strategy is an everyday challenge. We need to balance between the necessity of effectively controlling our impact on the environment and that of running our business in a way that will positively affect society, locally and globally, both at the financial and non-financial level.
Relating to raw material conservation, the Group invested in increasing the use of alternative raw materials in clinker, cement and concrete production. In the case of cement production, we not only worked towards the development of new blended types that will satisfy present and future needs of our customers, but also made efforts to introduce blended cement types in new markets and familiarize them with the benefits of their use. Using alternative raw materials helps to reduce the consumption of extracted raw materials as well as the amounts of by-products that have to be land filled. In the U.S.A., we implemented programs to collect concrete returns by our ready-mix facilities and use them for block production, aggregates for pavements and other uses. A similar program has been in place in Greece that takes concrete returns and uses them as raw materials for clinker production at our Kamari plant. Moreover, a pilot program, initiated in 2011, that covered the recycling of demolition wastes was continued in 2012 and extended to also cover the recycling of excavation wastes to be used as raw materials for clinker production. Moreover, our ST subsidiary provides solutions for managing fly ash minimizing the need, the cost and the risk associated with land filling and produces products that can be used either as alternative raw materials or for energy recovery.
Concerning energy efficiency, we augmented our efforts and continued to harmonize our actions across all of our operations, in order to increase the use of alternative fuels, especially biomass, and reduce the thermal energy consumption of our facilities. In line with acceptable best practices across our sector, an action plan was developed and implemented over the last several years. As part of this plan, the necessary investments were authorized for the acquisition and installation of the necessary, state-of-the-art equipment for the handling, storage and feeding of alternative fuels in many of our plants.
Nevertheless, local circumstances - such as the availability of waste treatment facilities, alternative markets for materials, and the infrastructure available to safely collect, manage and transport waste materials - influence our decisions. In many cases these conditions are not subject to TITAN’s control. Whenever possible, we took the opportunity to overcome such obstacles and create the supporting value chain. Such was the case in Bulgaria where a new business activity, in the form of our subsidiary company, GAEA, was initiated with the objective of sourcing and producing suitable alternative fuels for our plant. For more details, see the section in this Report on Innovation.
The prevailing conditions in the markets where we operate, namely Greece and Southeastern Europe, and the enduring economic recession resulted in a decreased demand for cement, shifting our focus onto new markets. These markets have different preferences in cement qualities and are characterized by low penetration of blended cements. As a consequence, the average Group clinker-to-cement ratio tends to increase, having an unfortunately negative effect on our specific CO2 emissions footprint.
Last but not least, changing political conditions, like those in Egypt, create a volatile environment that can affect not only our business plans but also our environmental performance. Setting restrictions on the supply of fuel is a good example of how such developments can have an adverse impact on CO2 emissions. Having to adopt alternative sources of energy, means that a fuel with a low emissions factor is being substituted for a fuel with a higher emission factor, thus increasing overall emissions. It is estimated that substituting natural gas with coal or pet-coke can increase our emissions by about 5.0%. We are continuously monitoring the unfolding situation and are preparing our response accordingly.